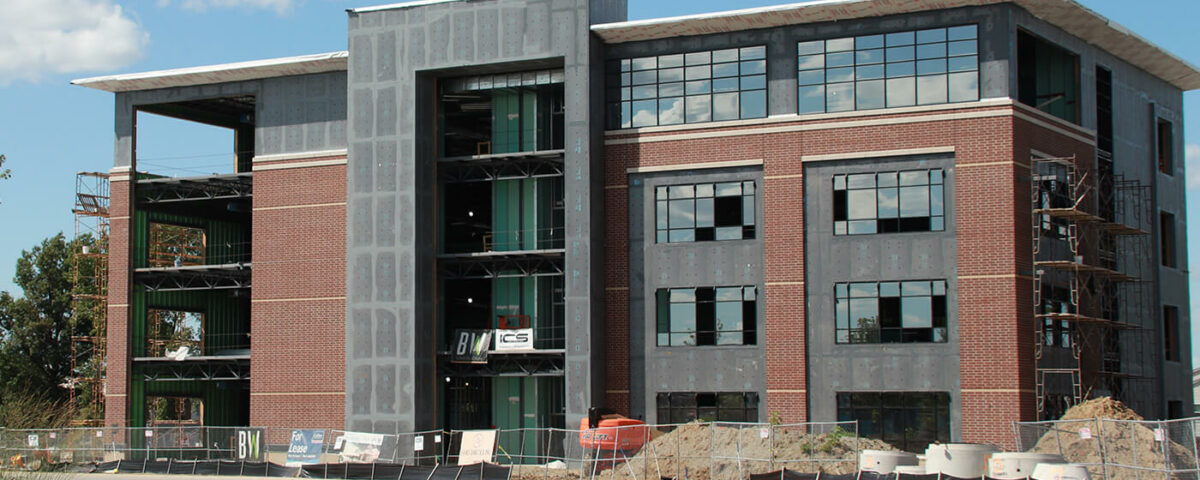
Client: BW Construction / North Ellipse
Budget: $10,000,000
Completed: May 2020
Details: North Ellipse is a four-story, 45,000 sf steel-frame structure located in the Fisher Nickel Plate District. The original phase was to complete the core and shell and then move to the build-to-suit office space for companies looking to expand or move to Fishers’ business community. The project also included additional site building to include a public parking lot. The exterior of the building was designed to meet the architectural expectations of the beautiful Nickel Plate District. Included in this project were 6 tenant buildouts, designed with the same architectural expectations of this district. Interior design teams for each buildout spent the time to be unique to the individual tenant and meet their demands for their space layouts.
James Babcock Inc was hired to perform electrical design-build services for the core and shell, site lighting, and interior tenant building for the 6 current tenants. Also, our company provided the design-build services for Fire Alarm, Security, Access Control, Fiber Optics, Communications Cabling, and Audio Visual.
Our first design focus was on the exterior building lighting. A minimum amount of exterior building illumination was required by local zoning. However, the architect wanted the main storefront illuminated to highlight the 4-story glass entrance. We installed cylinder, up/down fixtures on each side of and from ground level to the top of the structure. The same cylinders were used at the corners of the building providing just the right amount of building accent lighting. We also installed 15 streetlamp poles and 16 in-ground up-lights to provide the sidewalk lighting around the building.
Electrical rooms were built-out 100%. We prefabricated panels and conduit to save time on the tenant finish phases. The branch circuit cables were installed in the junction box and spliced to the wiring already installed in the panels.
The fast-paced construction scheduling really began when tenants leased a space, there was no time for delays. Covid-19 caused major shipping issues with desired lighting. We were able to install temporary light fixtures that would allow inspections to pass while we worked through the shipping delays. The tenants were able to occupy the spaces allowing us to return later and install the desired fixtures.
Overtime hours were constantly needed on the tenant finishes. We spaced our crew hours out to help by having our electrical, fire alarm, and systems crews all in the spaces along with the other trades to increase manpower and meet the fast-paced deadlines.